一、前言
交通在能源消耗和碳排放中占据重要地位,是引发石油消费增长的关键因素。发展节能环保的新能源汽车不仅可以减少石油进口、减少碳排放,也可以实现中国汽车行业转型升级。燃料电池汽车是新能源汽车中的一种,具有续驶里程长、燃料加注时间短、兼容可再生能源等特点,愈来愈得到各级政府、企业、研究机构的重视。各国政府纷纷推出激励与财政补贴政策促进燃料电池汽车初级市场的形成。燃料电池汽车逐渐从规模示范过度到商业化运行,以丰田Mirai、本田Clarity、现代Nexo为代表的率先商业化的燃料电池车在性能等方面已经达到了传统燃油车水平,乘用车的燃料电池功率级别一般在100kW 左右,商用车的燃料电池功率输出在30~200kW。上汽大通汽车有限公司的FCV80汽车是我国第一个开始销售的燃料电池车,其他车厂也纷纷推出燃料电池公告产品,从车型来看,大多集中在商用车,从功率级别看,国内车用燃料电池堆主要以30~50kW 为主,功率等级普遍低于国际同类燃料电池车,其原因从表面上看是企业在迎合财政补贴门槛,但从深层次方面看是我国高比功率技术与国际先进水平还有一定的距离(无论是目前引进的电堆还是本土电堆)。因此,有必要提高功率密度,尤其是在乘用车有限的空间内要装载一定功率的燃料电池堆更需要高的功率密度。另外,从降低成本的角度,提高功率密度可以降低燃料电池材料、部件等硬件消耗,进而可以显著地降低燃料电池成本。
提高燃料电池的功率密度需要从提高性能与减小体积两方面着手。在性能方面,从燃料电池极化曲线(见图1)分析可知,通过降低活化极化、欧姆极化、传质极化等多方面入手提高燃料电池性能,这就需要改进催化剂、膜、双极板等关键材料的性能,需要保障电堆的一致性等;在体积方面,需要降低极板等硬件的厚度,提高集成度等。本文将从理论分析及工程实践经验着手,探讨提高功率密度的有效途径,供从事本领域的研究人员及工程技术人员参考。
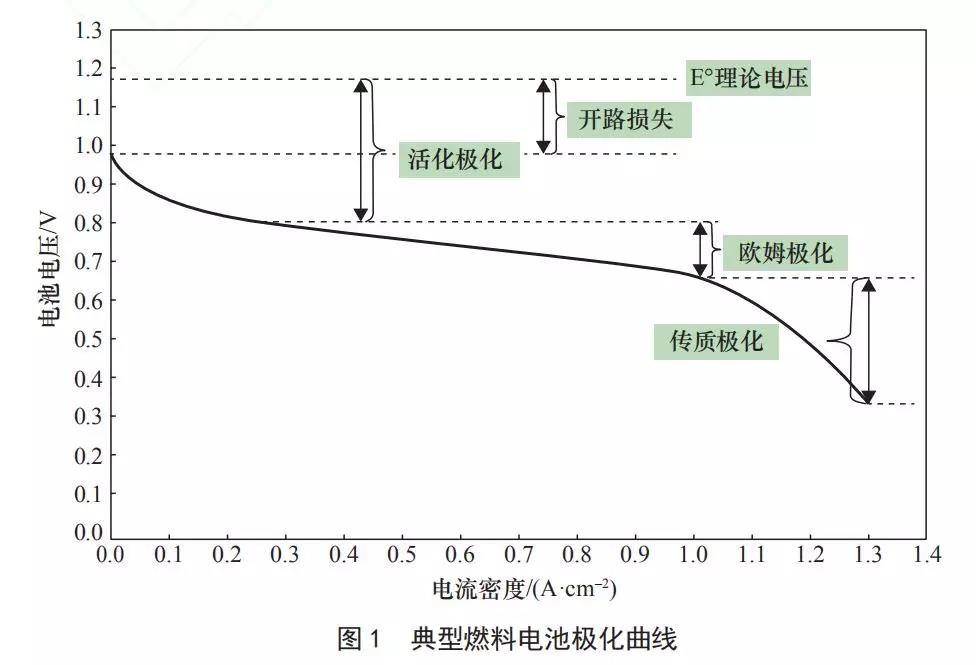
二、高活性、高稳定性催化剂与电极
从燃料电池极化曲线可以看出,提高燃料电池性能首先要降低活化极化,而活化极化主要与催化剂活性密切相关。燃料电池在反应过程中,由于氧还原反应(ORR)的交换电流密度远低于氢氧化反应(HOR),一般极化损失主要来自于阴极侧(空气侧)。因此,研究焦点是提高阴极侧催化剂的活性。目前,质子交换膜燃料电池中常用的商用催化剂是铂炭催化剂(Pt/C),是由 Pt 的纳米颗粒分散到碳粉(如 XC-72)载体上的担载型催化剂,实际使用测试发现这种商用催化剂在活性、稳定性等方面都存在一定不足。美国能源部(DOE)催化剂指标如表1所示,研究者通过Pt晶面控制、Pt-M合金催化剂、Pt-M核壳催化剂、Pt表面修饰、Pt单原子层催化剂等多种途径探索高活性、高稳定性催化剂的解决方案,在这些研究中目前可以实际应用的只有Pt-M合金催化剂。
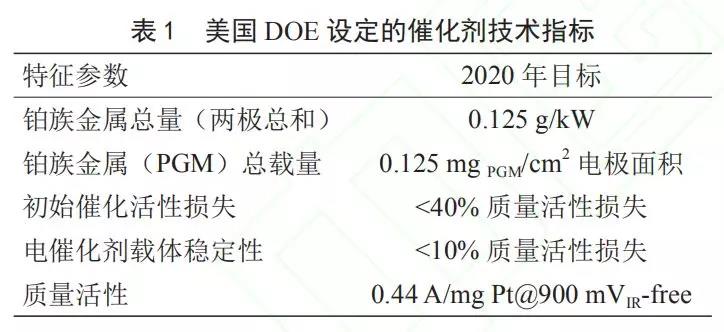
Pt-M催化剂是Pt与过渡金属形成的合金催化剂,通过过渡金属催化剂对Pt的电子与几何效应,在提高稳定性的同时,质量比活性也有所提高;同时,降低了贵金属的用量,使催化剂成本也得到大幅度降低。 如Pt-Co/C、Pt-Fe/C、Pt-Ni/C等二元合金催化剂,展示出了较好的活性与稳定性。Chen 等人利用铂镍合金纳米晶体的结构变化,制备了高活性与高稳定性 Pt3Ni 纳米笼催化剂,其质量比活性与面积比活性分别提高36倍与22倍。在Pt合金催化剂应用方面,丰田汽车公司披露了在所发布的商业化燃料电池车Mirai上就是采用了Pt-Co合金催化剂,使其催化剂活性提高了1.8倍。中国科学院大连化学物理研究所(大连化物所)开发的Pt3Pd/C催化剂已经在燃料电池电堆得到了验证,其性能可以完全替代商品化催化剂;此外,大连化物所还研制出了超小PtCu合金催化剂,其质量比活性是目前Pt/C的3.8倍;PtNi 纳米线合金催化剂质量与面积比活性分别达到Pt/C的2.5倍和 3.3 倍(见图2),展示了较好的应用前景。
目前,针对Pt-M催化剂,需要解决燃料电池工况下过渡金属的溶解问题,金属溶解不但降低了催化剂活性,还会产生由于金属离子引起的膜降解问题。因此,提高 Pt-M 催化剂的稳定性问题还需要进一步研究。Pt 合金催化剂的稳定性保障,除了提高自身的稳定性以外,还要从系统控制策略出发,减少催化剂的衰减工况,对提高催化剂稳定性起到重要作用。
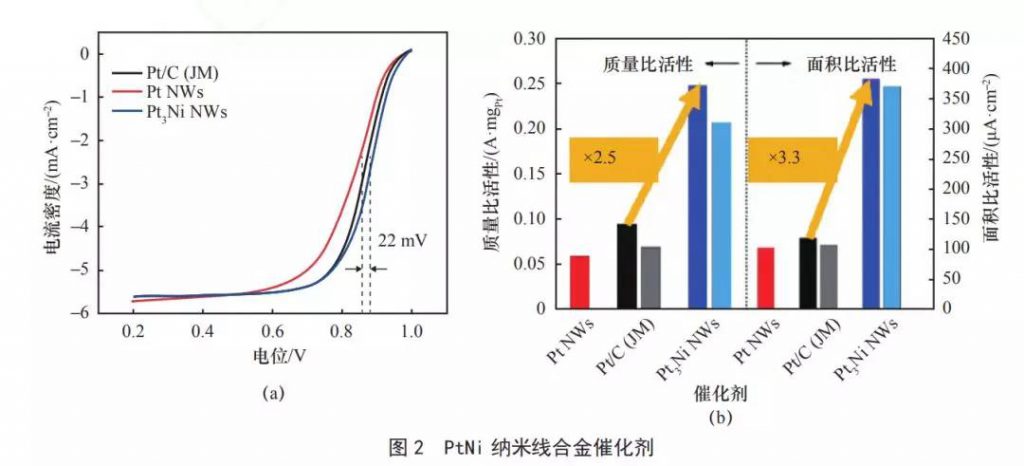
除了提高催化剂活性、减少活化极化外,电极结构对性能提升也非常重要。电极通常由扩散层与催化层组成,设计合理的电极结构有利于降低欧姆极化与传质极化。电极的发展趋势是利用进一步减薄催化层厚度来提高反应效率,提高气体扩散层的传质通量,改善传质过程,进而提高电极的极限电流密度,使工作电流提升达到2.5~3A/cm2 或更高。丰田汽车公司的Mirai燃料电池堆就是采用了薄的低密度扩散层,明显地减少了欧姆极化与传质极化,使工作电流密度得到大幅提升。
三、增强复合薄膜
从图1可见,提高性能除了要通过提高催化剂活性降低活化极化外,随着电流增大,伏安曲线直线段的斜率主要是欧姆极化决定的,其中膜的欧姆极化占有主要份额。为了提高性能,目前车用质子交换所用的膜逐渐趋于薄型化,由几十微米降低到十几微米或以下,以降低质子传递的欧姆极化,获得较高的性能。但是薄膜在车载运行工况下(如操作压力、干湿度、温度等操作条件的动态变化)更容易受到机械损伤与化学降解。复合膜是由均质膜改性而来的,它利用均质膜的树脂与有机或无机物复合使其比均质膜在某些功能方面得到强化。因此,增强复合薄膜是解决薄膜应用的主要解决方案。增强复合膜既保证了薄膜的性能又使其机械强度及化学耐久性得到强化,其实现的技术途径一是机械增强;二是化学增强(见图3)。
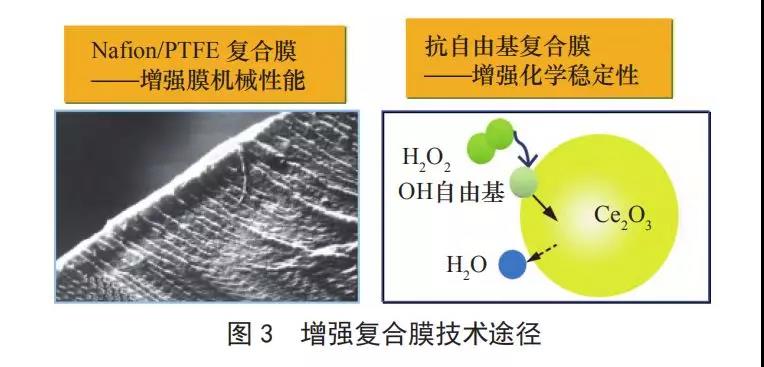
机械增强膜如以多孔薄膜(如多孔PTFE)或纤维为增强骨架、浸渍全氟磺酸树脂制成复合增强膜,分布于贯穿多孔膜之间的树脂保证了质子传导,多孔基膜使薄膜的强度提高,同时尺寸稳定性也有大幅改善,如美国戈尔公司的复合膜、中国大连化物所的专利技术 Nafion/PTFE 复合增强膜和碳纳米管增强复合膜等。化学增强是为了防止由于电化学反应过程中自由基引起的化学衰减,加入自由基淬灭剂可以在线分解与消除反应过程中的自由基,提高耐久性。大连化物所采用在Nafion膜中加入1wt.%的CsxH3−xPW12O40/CeO2 纳米分散颗粒制备出了复合膜,利用CeO2中的变价金属可逆氧化还原性质淬灭自由基,CsxH3−xPW12O40 的加入在保证了良好的质子传导性同时还强化了H2O2催化分解能力。南京大学在质子交换膜中加入抗氧化物质维生素E,其主要成分α-生育酚不仅能够捕捉自由基变为氧化态,而且能够在渗透的氢气帮助下,重新还原,从而提高了燃料电池寿命。
四、双极板流场与材料
双极板是燃料电池的重要部件,其作用是支撑膜电极并具有传导电子、分配反应气并带走生成水。因此,双极板在燃料电池性能方面,除了影响欧姆极化外还会影响传质极化。
从降低欧姆极化方面考虑,双极板要具有良好的电子传导性。目前常用的双极板包括石墨材料、石墨复合材料、金属材料,这三种双极板材料均具有良好的导电性,但针对不同的应用场景要有一些特殊考虑。纯石墨双极板导电性好,但通常要机械雕刻出流道,加工效率低、成本高,是第一代双极板技术,已逐渐被取代。石墨复合材料通常是采用碳粉与树脂等组分按一定比例混合制成的,可以通过模压方法加工流场,具有良好的经济性;但树脂等非导电性物质的加入会在一定程度上影响导电性,尤其是在大电流密度下表现明显,不利于提高功率密度;因此,石墨复合材料要在保证双极板的致密性、可加工性基础上尽可能提高导电性。
金属是电与热的良导体,其作为双极板材料得到越来越普遍的应用,尤其是车辆空间限制(如乘用车),要求燃料电池具有较高的功率密度。薄金属双极板以其可以实现双极板的薄型化及本征的优良导电特性,成为了提高燃料电池功率密度的首选方案;目前各大汽车公司大都采用金属双极板技术,如丰田汽车公司、本田株式会社、现代汽车有限公司等。金属双极板技术挑战是其在燃料电池环境下(酸性、电位、湿热)具有耐腐蚀性且对燃料电池其他部件与材料的相容无污染性。目前常用的金属双极板材料是带有表面涂层的不锈钢或钛材。针对燃料电池不锈钢双极板表面耐腐蚀涂层技术,国内外进行了大量的学术研究工作,其涂层材料要保证耐腐蚀、导电兼备性能,代表性的涂层材料如表2所示。总体来说,表面涂层材料可以分为金属、金属化合物与碳涂层三类;金属类包括贵金属以及金属化合物。贵金属涂层,如金、银、铂等,尽管成本高,但由于其优越的耐蚀性以及与石墨相似的接触电阻使其在特殊领域仍有采用。为了降低成本,处理层的厚度尽量减薄,但是要避免针孔。金属化合物涂层是目前研究较多的表面处理方案,如Ti-N,Cr-N,Cr-C 等表现出较高的应用价值。除了金属类涂层以外,在金属双极板碳类膜方面也有一定探索,如石墨、导电聚合物(聚苯胺、聚吡咯)以及类金刚石等薄膜,丰田汽车公司Ce2O3H2O 的专利技术(US2014356764)披露了具有高导电性的 SP2 杂化轨道无定型碳的双极板表面处理技术。
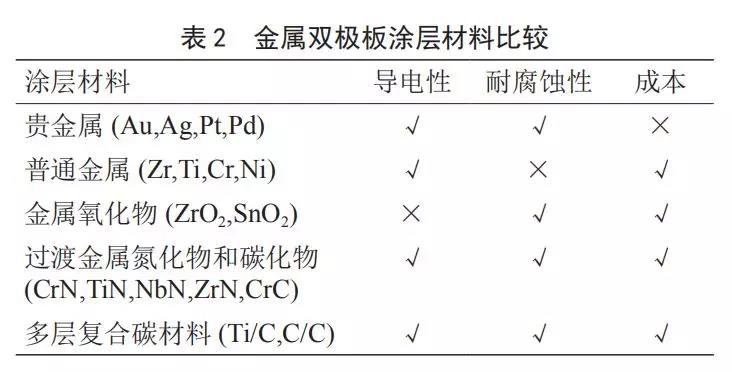
除了涂层材料,涂层的制备技术也是提高其耐蚀性、保证导电性的重要因素。涂层要做到无针孔、无裂痕等;金属双极板表面处理层的针孔是双极板材料目前普遍存在的问题,由于涂层在制备过程中的颗粒沉积形成了不连续相,从而导致针孔的存在,使得在燃料电池运行环境中通过涂层的针孔发生了基于母材的电化学腐蚀。另外,由于涂层金属与基体线胀系数不同,在工况循环时发生的热循环会导致微裂纹,也是值得关注的问题,选用加过渡层方法可以使问题得到缓解。大连化物所与大连理工大学合作进行了金属双极板表面改性技术的研究,采用了脉冲偏压电弧离子镀技术制备多层膜结构,结果表明多层结构设计可以提高双极板的导电、耐腐蚀性。
合理的双极板流场设计与布局,可以起到降低传质极化作用,有利于提高大电流密度下的性能,进一步提高电堆的功率密度。丰田汽车公司在Mirai 燃料电池车电堆中推出了3D流场新型设计理念(见图 4),改变了传统蛇型、平行沟槽型的2D流场构型,使流体有垂直于乙醇胺(MEA)气体扩散层与催化层的分量,反应物与生成物不是单纯依靠浓差扩散到达与脱离反应界面,而是有强制对流作用,极大地改善了燃料电池传质推动力,性能得到显著提升。此外,这种3D流场具有一定的储水功能,有利于燃料电池运行时的湿度调整,可以提高低增湿下燃料电池性能。
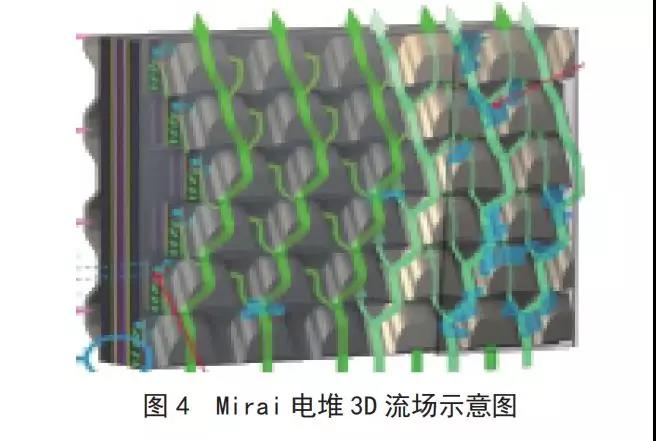
通过模拟计算可以更进一步证实3D流场强化了流道、扩散层的排水能力(见图 5,3D 流场在扩散层内出现了水的零饱和区),同时增加了氧气在催化层的强制对流,尤其在高电流时与2D常规平行沟槽流场比较,燃料电池性能有了很大的提升。
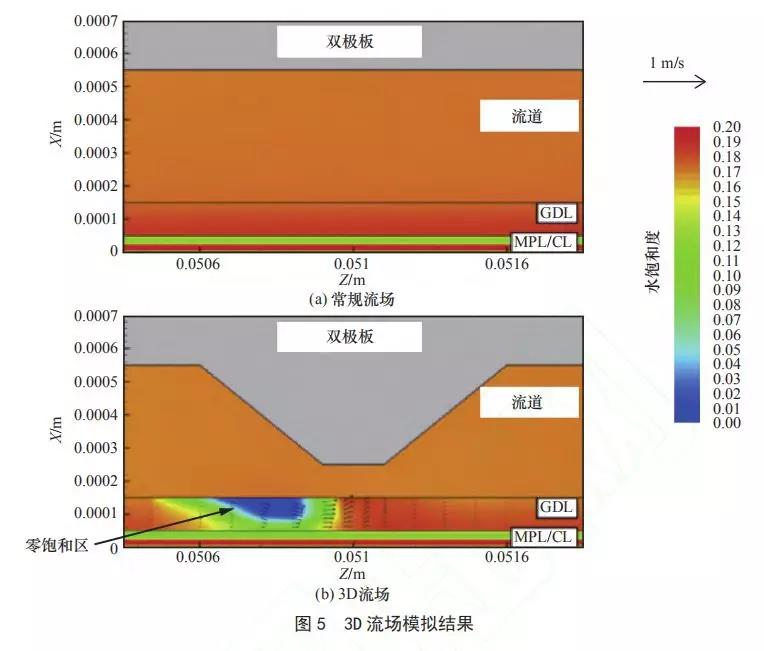
五、电堆组装与一致性
电堆组装与一致性对电堆性能的提高至关重要。组装决定电堆部件之间的配合程度,组装良好的电堆才能最大发挥部件的性能;一致性是衡量电堆性能优劣的重要指标,一致性好的电堆可以在大电流密度下工作,有利于提高电堆的功率密度。
电堆组装过程通常是在压力机上进行的,一般是依据一定的组装顺序及定位方法,把MEA与双极板摞装起来并附以集流板、端板,通过紧固装置固定形成一个完整的电堆。电堆组装除了要保证电堆密封性外,还要保证 MEA 与双极板界面的良好接触。电堆设计阶段要考虑电堆密封元件形变与MEA 形变的匹配,在组装过程中通过控制电堆高度定量双极板向膜电极扩散层中嵌入深度,并同时使密封元件达到预定的变形量。图6为电堆组装过程密封件、双极板与 MEA 相对位置图,电堆组装高度为h=h1=h2,其中h1为满足MEA压深以获得预期较小接触电阻的组装高度;h2为满足密封变形要求的组装高度,一般通过离线试验可以确定获得较小接触电阻 MEA 的压深率 fM 和密封件压缩率fr,密封件压缩率fr根据密封结构与材料可在一定范围内调整(如30%~60%)。
h1 = [bM1(1–fM) + bb]·n+K (1)
h2 = [2d(1–fr) + (bb–2C) + bM2]·n+K (2)
式(1)、(2)中:fr为密封件压缩率;fM为双极板对MEA压深率;bb为双极板的厚度;n为电堆中单电池节数;K为其他硬件如集流板、端板等的厚度。
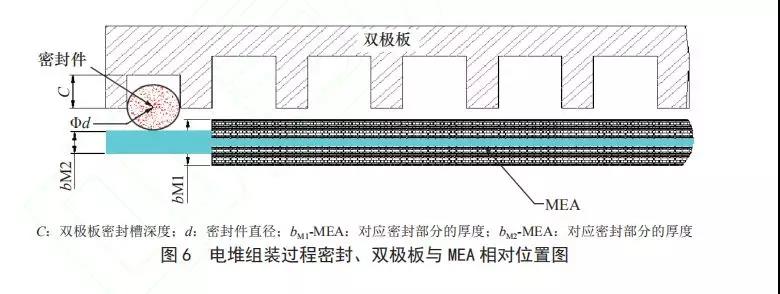
除了用高度控制来获得电堆最佳组装匹配外,还可以采用组装力控制法确定电堆部件之间的良好匹配关系。组装力可以通过组装机械如油压机实施,随着组装力加大,双极板与 MEA 间的接触逐渐减少,当达到平缓区即为最佳的组装力控制区(见图7),通常接触电阻与组装力的关系可以在电堆组装前通过单电池试验离线获得,并确定接触电阻达到较小状态对应的组装力。
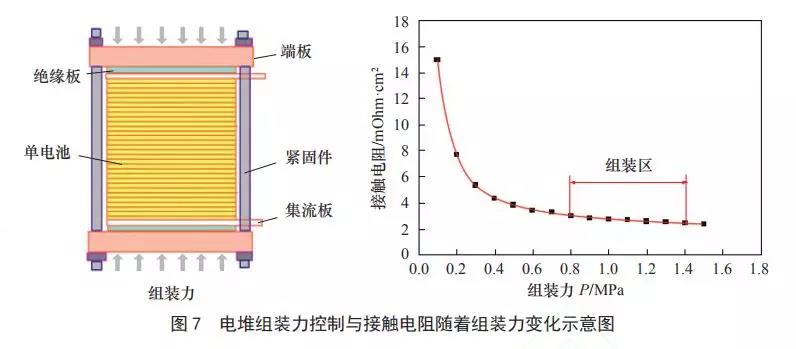
燃料电池堆的一致性是提高电堆功率密度的基本保障。一致性表示电堆单电压偏离平均单电压程度;一致性好的电堆,可以实现电流同步放电。如果电堆一致性不好,存在个别节单电压偏低,当电流进一步加大时可能会导致反极。在安全角度操作过程中要避免反极的出现,一般电堆系统或测试台架中都要设有低电压保护。因此,提高一致性,电堆就可以同步在较高的电流密度下工作,实现功率密度的提高。
电堆一致性与电堆设计、制造、操作等因素密切相关。在设计方面,要考虑降低其结构对可能产生几何误差的敏感度,保证流体分配的均一性;在制造方面,要考虑材料均一性、控制加工精度,保证初始性能一致性;在操作方面,要避免布局水淹、欠气、局部热点的发生,保证操作性能一致性;此外,要注意电堆边缘可能产生的温度不均、流体分配不均问题,避免产生边缘单节过低现象。
大连化物所在其愈四十年的研发特别是最近几年的快速发展过程中,针对高比功率电堆技术,研究工作重点聚焦在催化剂、电极技术和材料、膜电极、流场、双极板、电堆结构、电堆运行管理、检测与控制等方面,开发出了高性能增强型复合质子交换膜,提高了车辆工况的适应性;以不锈钢为基材提出了金属双极板材料表面耐腐蚀、导电处理涂层方案,易于提高体积比功率;发展了基于静电喷涂的连续导通模式(CCM)制备技术,单位功率密度性能得到大幅提升;在电堆结构方面,从设计、制备、操作三方面进行调控,通过模拟仿真手段研究流场结构、阻力分配对流体分布的影响,厘清关键要素,探明了水的传递、分配与水生成速度、水传递系数、电极/流场界面能之间的依赖关系,掌握了稳/动态载荷条件对电堆阻力的影响,保证电堆在运行过程中保持均一性电堆具有很好的一致性,工作电流密度超过2.0 A/cm2,基于上述技术目前所开发的电堆功率密度可以达到3.0 kW/L(见图8,表3)。
六、结语
习近平主席指出:发展新能源汽车是我国从汽车大国走向汽车强国的必由之路。燃料电池车以其自身特有的优势正在成为新能源汽车的众目所注。然而,实现燃料电池车的大规模商业化还需要解决一些瓶颈问题,如加氢基础设施问题、政策法规问题等;在技术方面,还要进一步提高燃料电池性能、降低成本、提高耐久性等。燃料电池电堆是燃料电池汽车的核心,其比功率是代表电堆技术水平的重要指标。提高电堆比功率,不仅可以提高车辆的动力性能,而且,在同样功率输出情况下,高比功率电堆也可以大幅降低燃料电池硬件成本。除采用高活性催化剂、薄增强复合膜、导电耐腐蚀双极板等创新性材料实现燃料电池堆高比功率性能外,电堆结构优化也应同步考虑,如通过 3D 流场可以改善大电流的传质极化,优化组装过程可以有效降低欧姆极化,提高电堆的一致性有利于保证电堆高功率输出,这些措施都可以促进燃料电池堆性能的提高,有利于燃料电池堆比功率的提升。当然,燃料电池堆在性能、比功率提高的同时,更要关注其耐久性与成本。高性能、长耐久性与低成本是燃料电池实现商业化的关键因素。